· 研发中心 · 最新研究 · 11 分钟
数实融合,赋能未来:激发数字经济新动能,智能安全管理引领起重设备全生命周期革新
2025年3月5日上午,十四届全国人大三次会议开幕。李强总理作政府工作报告。在“2025年政府工作任务”中指出激发数字经济创新活力。
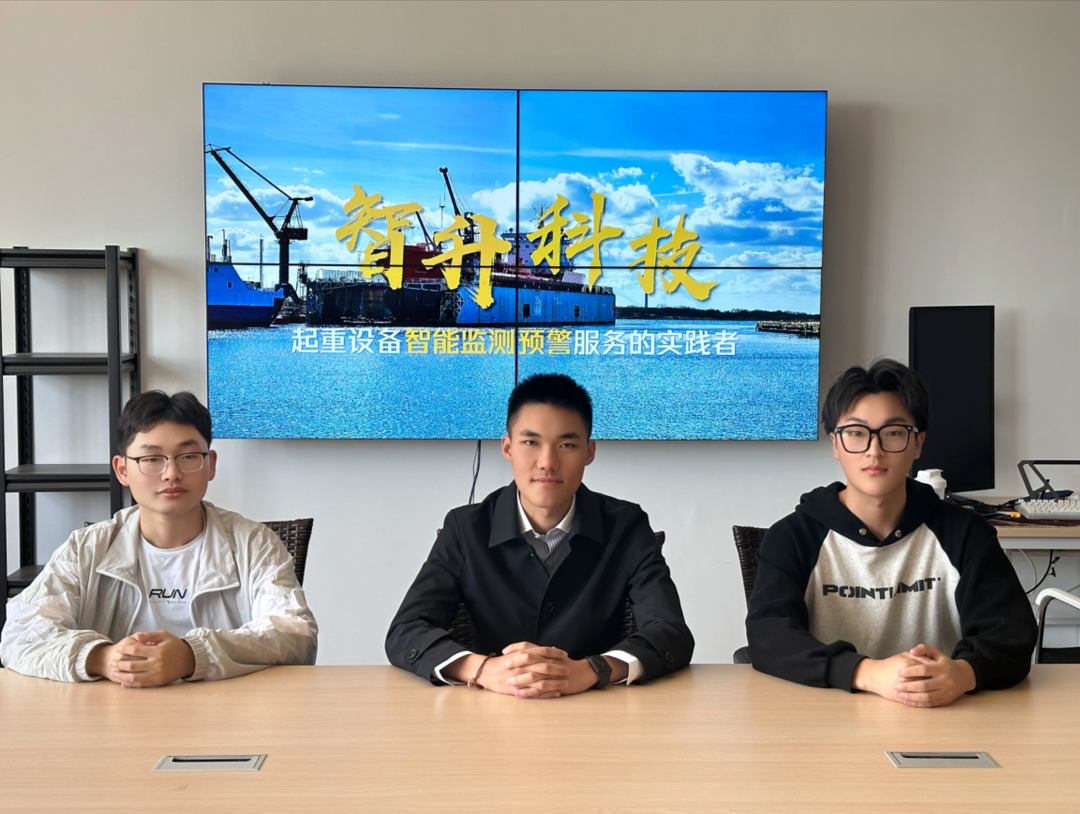
2025年3月5日上午,十四届全国人大三次会议开幕。李强总理作政府工作报告。在“2025年政府工作任务”中指出激发数字经济创新活力。持续推进“人工智能+”行动,将数字技术与制造优势、市场优势更好结合起来,支持大模型广泛应用,大力发展智能网联新能源汽车、人工智能手机和电脑、智能机器人等新一代智能终端以及智能制造装备。
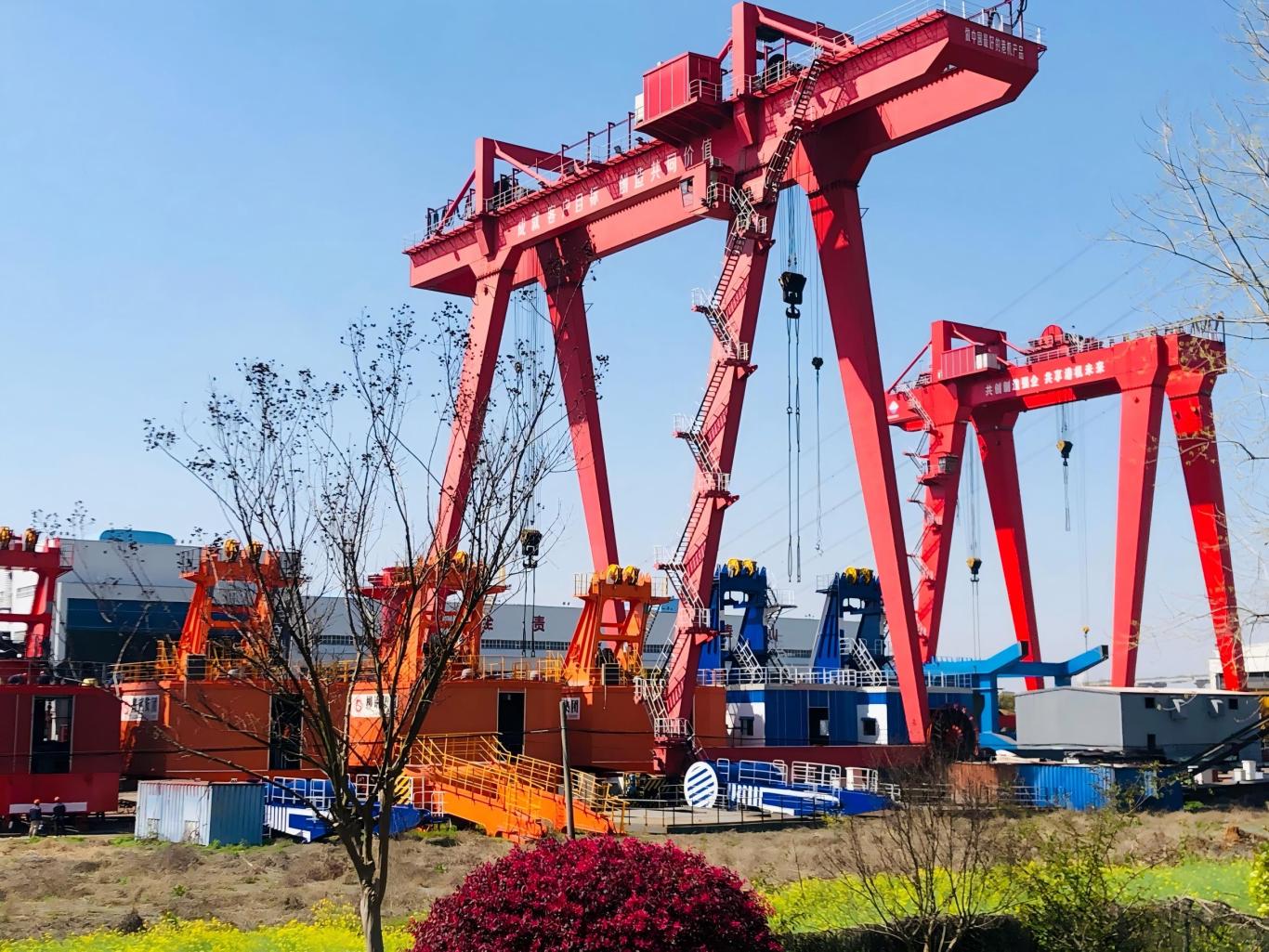
本项目是一套融合人工智能(AI)、工业物联网(IIoT)和云计算的智能安全管理方案,专为塔式起重机、桥式起重机、门式起重机、履带吊车、汽车吊车等多种起重设备设计。系统通过多传感器融合(载荷、倾角、风速、温湿度、震动等),实现设备的实时监测、远程管理和智能预警,确保作业安全。
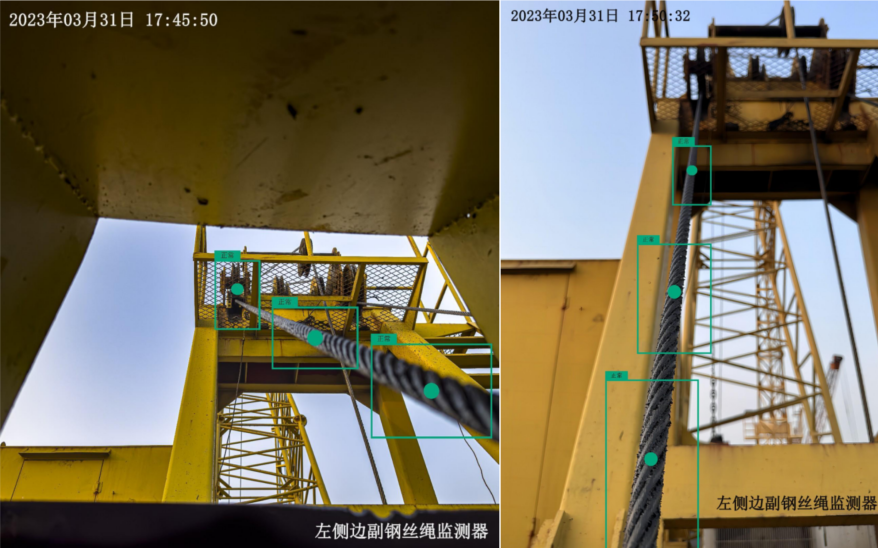
该系统具备智能预警和预测性维护能力,利用AI算法分析设备运行数据,提前识别超载、碰撞、风速过大、异常振动等安全隐患,并通过云端实时通知管理人员,避免安全事故发生。同时,系统支持远程监控与运维,管理人员可通过PC端或移动端随时查看设备状态,并实现智能派单与远程诊断,减少人工巡检成本,提高设备使用效率。
据统计,在2023年结案的特种设备事故中,约84.4%是由于使用管理不当(如违章操作、无证上岗、维护缺失、管理不善等)引发,另有约15.6%源于设备缺陷或保养不到位导致安全部件失效。
结合上述事故案例可以看到:超载违章操作、现场监控薄弱、设备带病运行等问题反复出现。团队耗时三年,走遍南京大小码头、港口、设备生产厂家,广泛听取企业的反馈后,总结出当前核心需求。
当前市场上的智能监测系统多集中于实时数据采集和报警功能,但缺乏从设备出厂、安装调试、日常使用、维护保养、到最终报废的全生命周期管理体系。
传统设备管理依赖人工巡检,维护记录分散,设备运行状态无法形成完整的数据链,导致事故预防和维护计划难以优化。
本项目通过AI+工业物联网技术,构建“设备健康档案”,利用大数据分析预测设备寿命,并提供智能运维建议,实现设备全生命周期安全管理。
市场上现有的起重设备监测系统大多由单一设备制造商开发,数据协议封闭,难以兼容不同品牌和型号的设备。施工企业、港口、制造业往往使用多种起重机,但不同设备的数据无法互联,形成数据孤岛,管理难度大。
本项目采用标准化工业协议和自适应数据融合技术,可兼容各大品牌和型号的起重设备,实现跨平台数据整合和统一管理,为企业提供全局化的安全管理解决方案。
现有智能监测系统的AI预警功能较为单一,往往基于固定阈值判断异常,无法适应不同工况下的动态安全需求。例如,设备在高温、高湿、高风速、复杂地形等环境下,安全阈值应动态调整,否则容易出现误报或漏报。
本项目采用自学习AI算法和环境感知技术,结合实时工况调整监测模型,减少误报和误触发率,确保报警精准度,真正做到“按环境适配,按工况调整”,为不同行业提供更精准的安全保障。
在第一次项目可行性研讨会中,项目创始人首次提出“起重设备智能监测预警集成系统”这一概念。
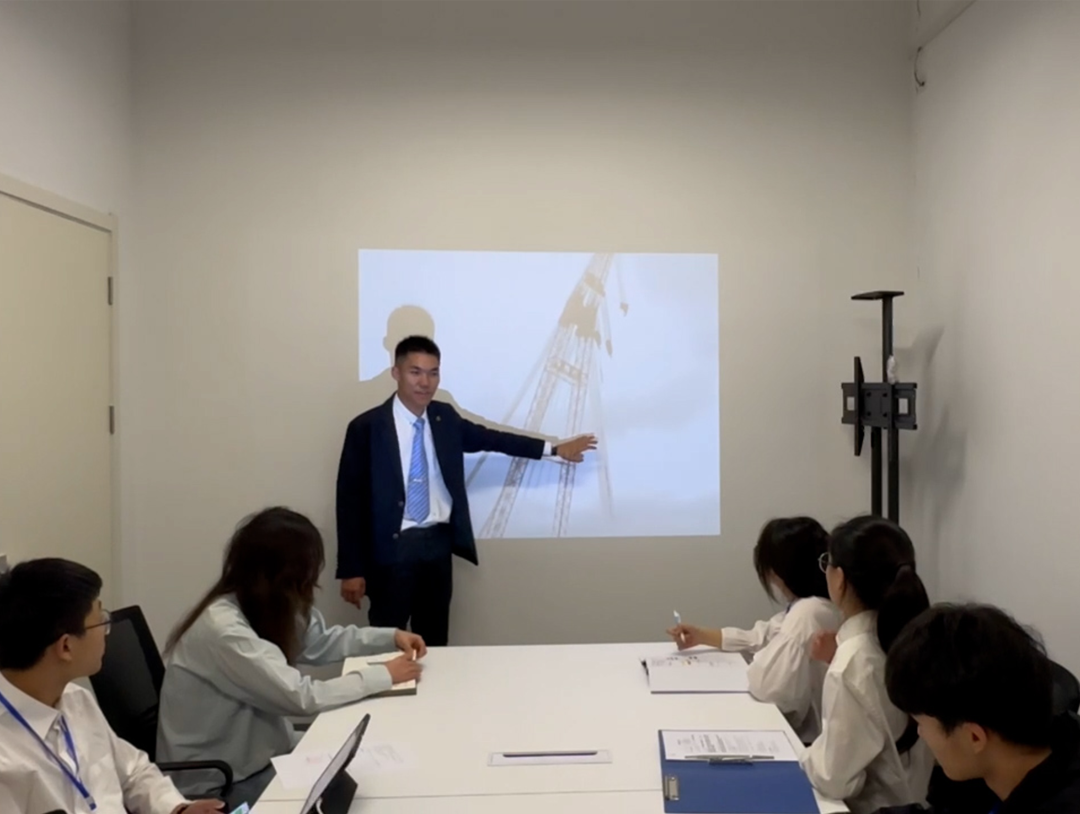
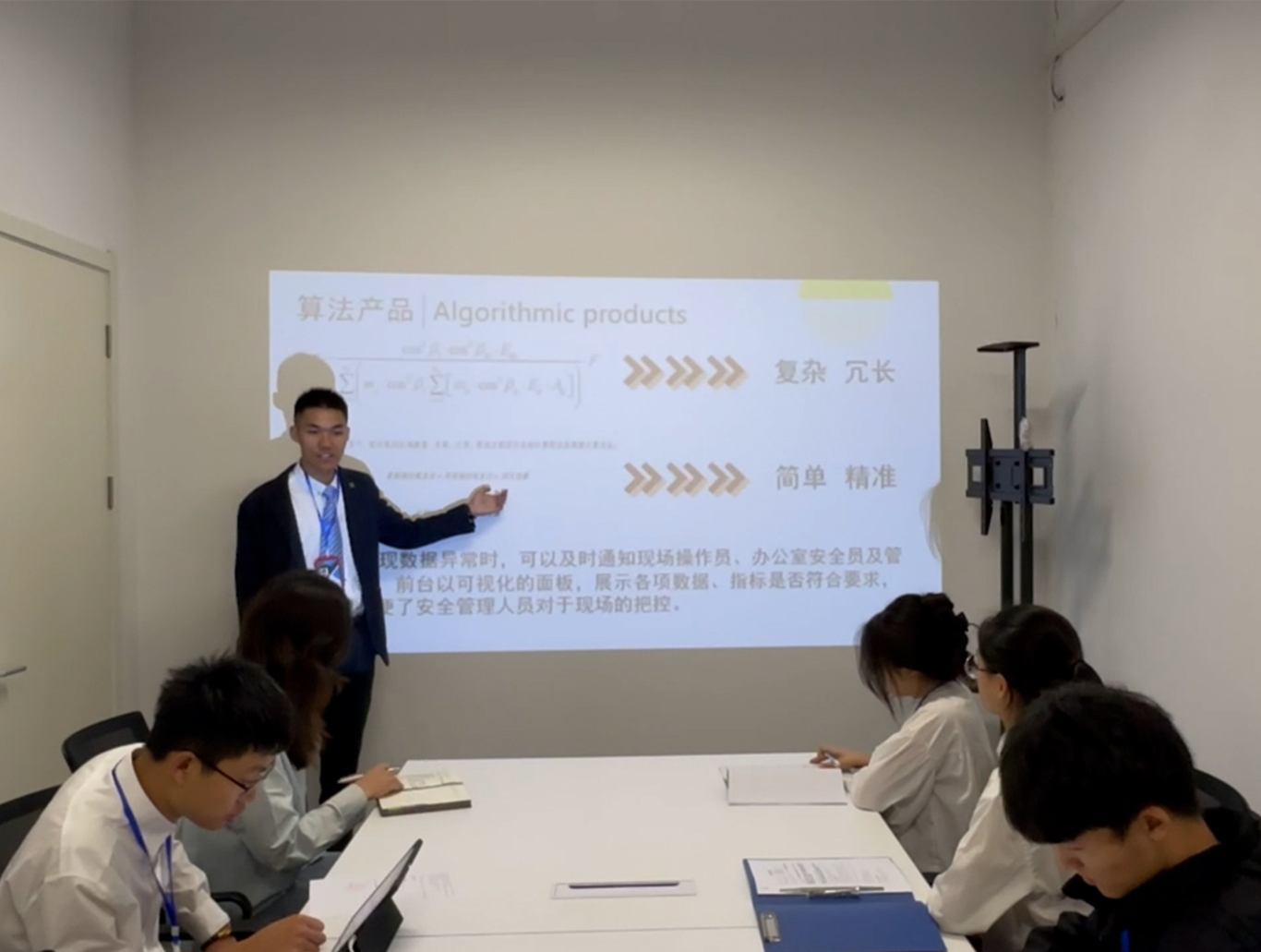
此后,团队迅速展开了深入讨论和调研,明确了项目的核心目标——利用先进的传感器技术、大数据分析和人工智能算法,实现对起重设备全方位、实时的监控与预警。
团队前往金港科创园,寻求行业前辈的帮助。到达金港科创园后,团队首先参观了园区内的高科技展示中心和多家专注于工业设备智能化的企业,并与几位拥有丰富实践经验的资深专家进行了面对面交流。
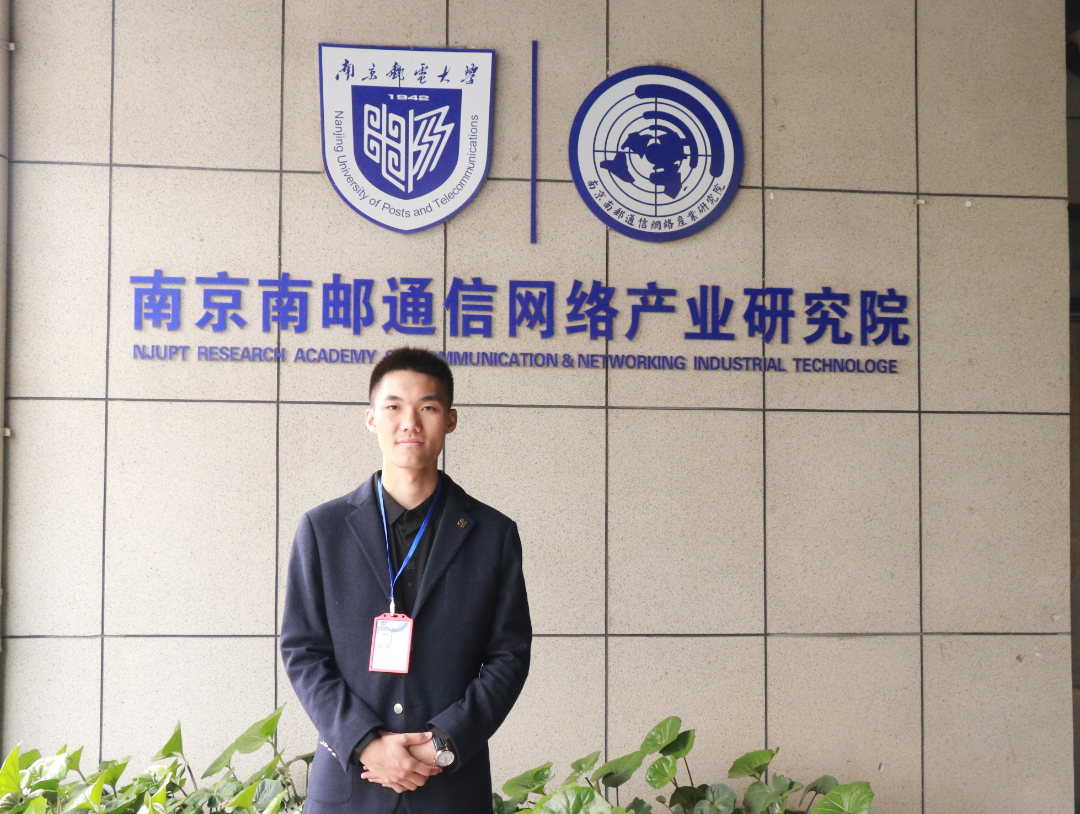
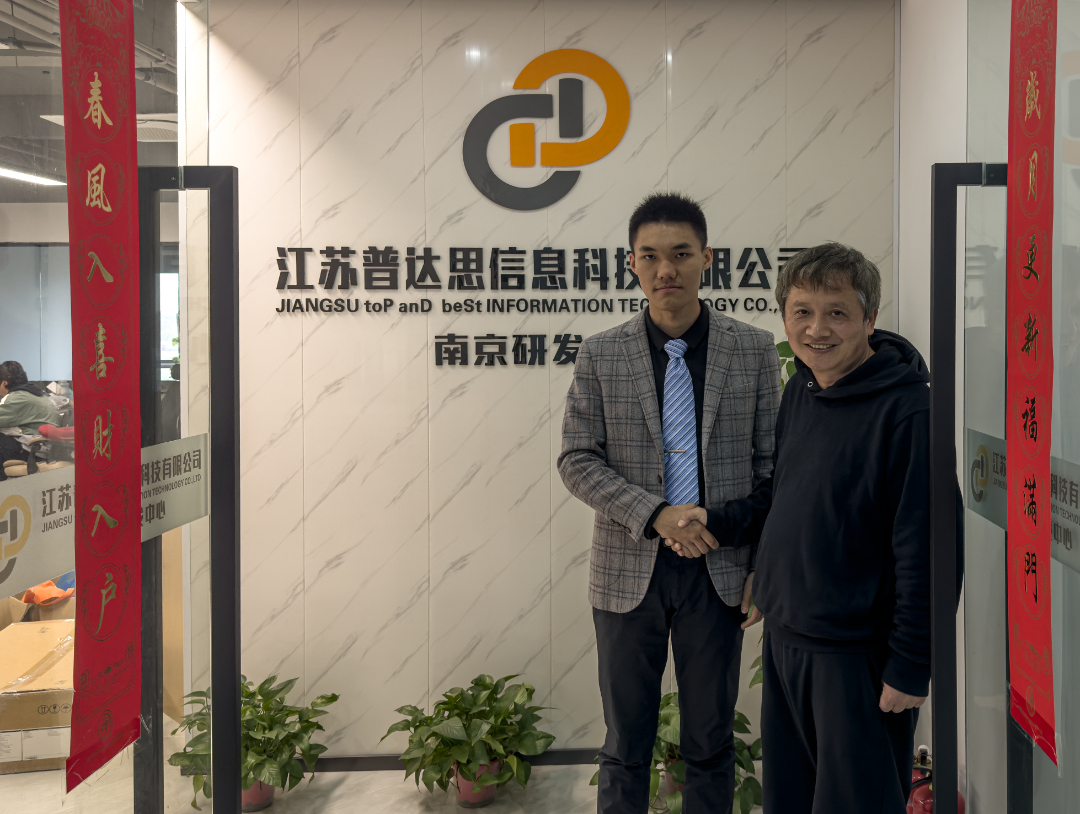
在交流过程中,专家们详细介绍了当前起重设备在实际运营中遇到的各类问题,并针对数据采集、实时监控以及预警机制等关键环节提出了多项建设性意见,同时分享了他们在设备维护与安全管理中的宝贵经验。
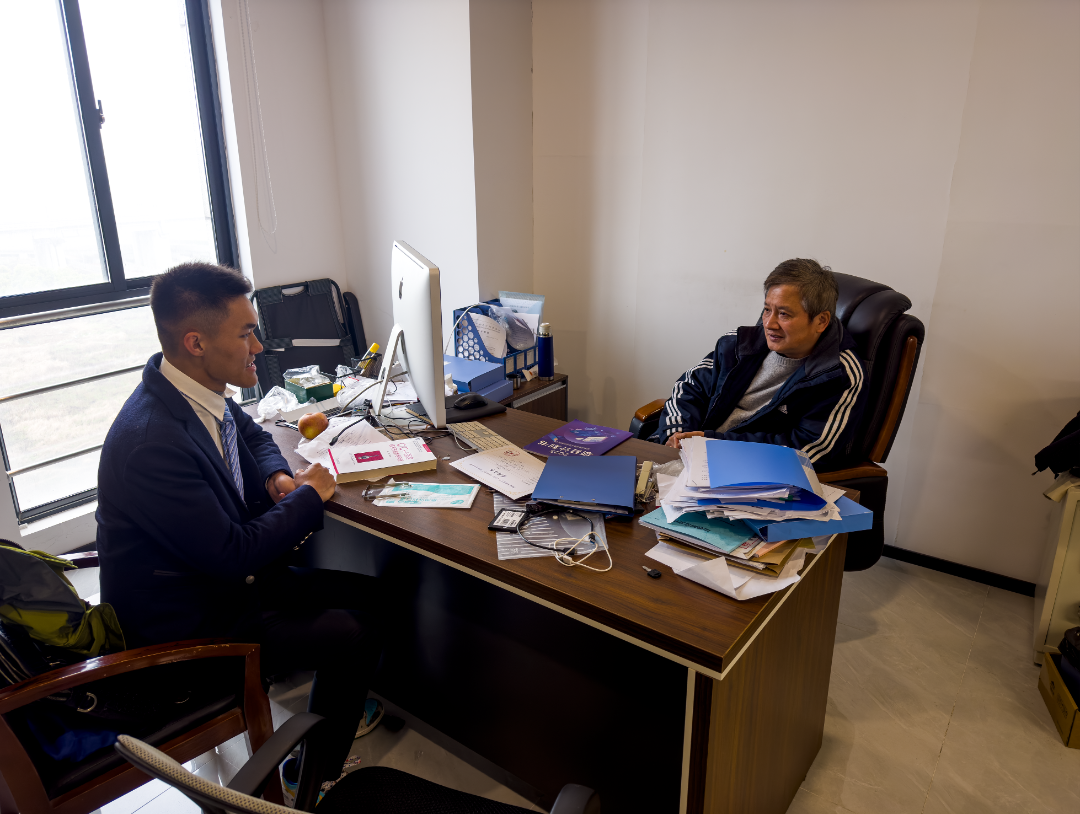
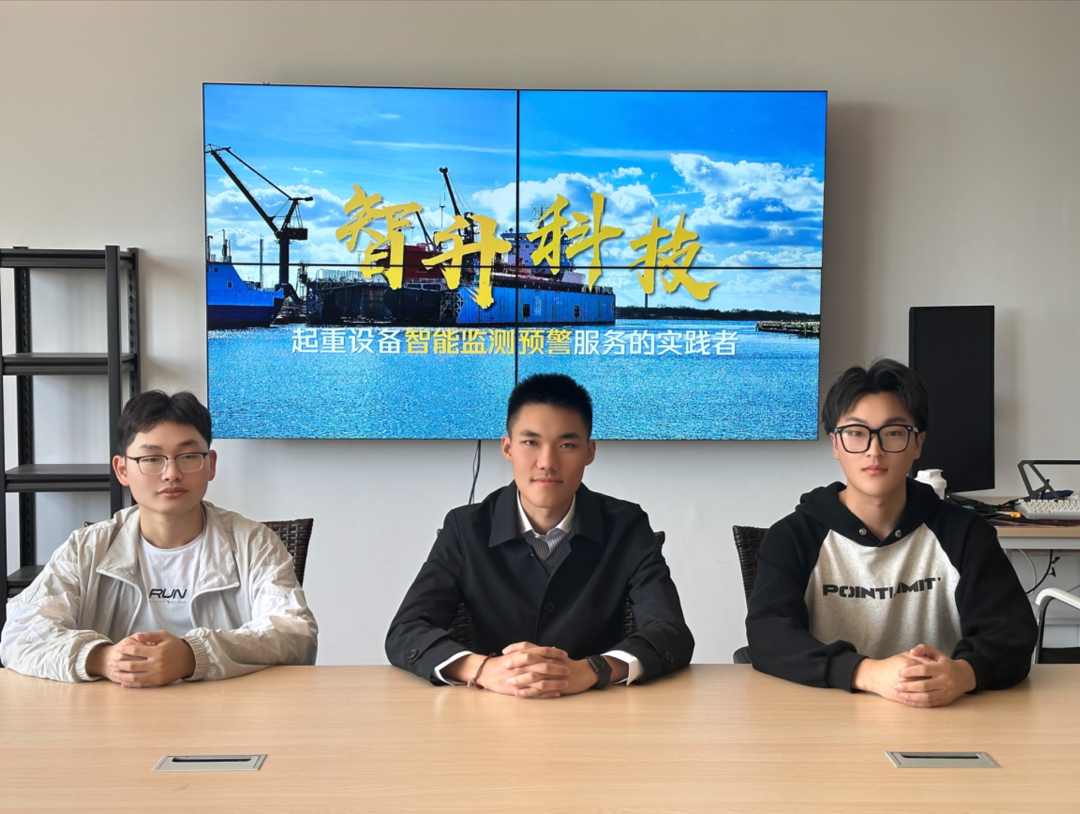
在交流过程中,专家们详细介绍了当前起重设备在实际运营中遇到的各类问题,并针对数据采集、实时监控以及预警机制等关键环节提出了多项建设性意见,同时分享了他们在设备维护与安全管理中的宝贵经验。
受益于这些前瞻性的建议,团队迅速调整了原有方案,对系统的技术架构和功能模块进行了优化,进一步明确了在严苛工况下确保设备稳定性和数据准确性的技术路径。
在确认项目初步可行性后,我们迅速联系了权威的查新机构。团队紧锣密鼓地展开了相关工作,对国内外最新技术、专利及市场趋势进行了全方位调研与比对。经过多轮论证,查新机构在最终报告中明确确认了产品的独特创新点和核心竞争优势,为项目后续的研发和市场布局提供了坚实的理论支撑和信心保障。
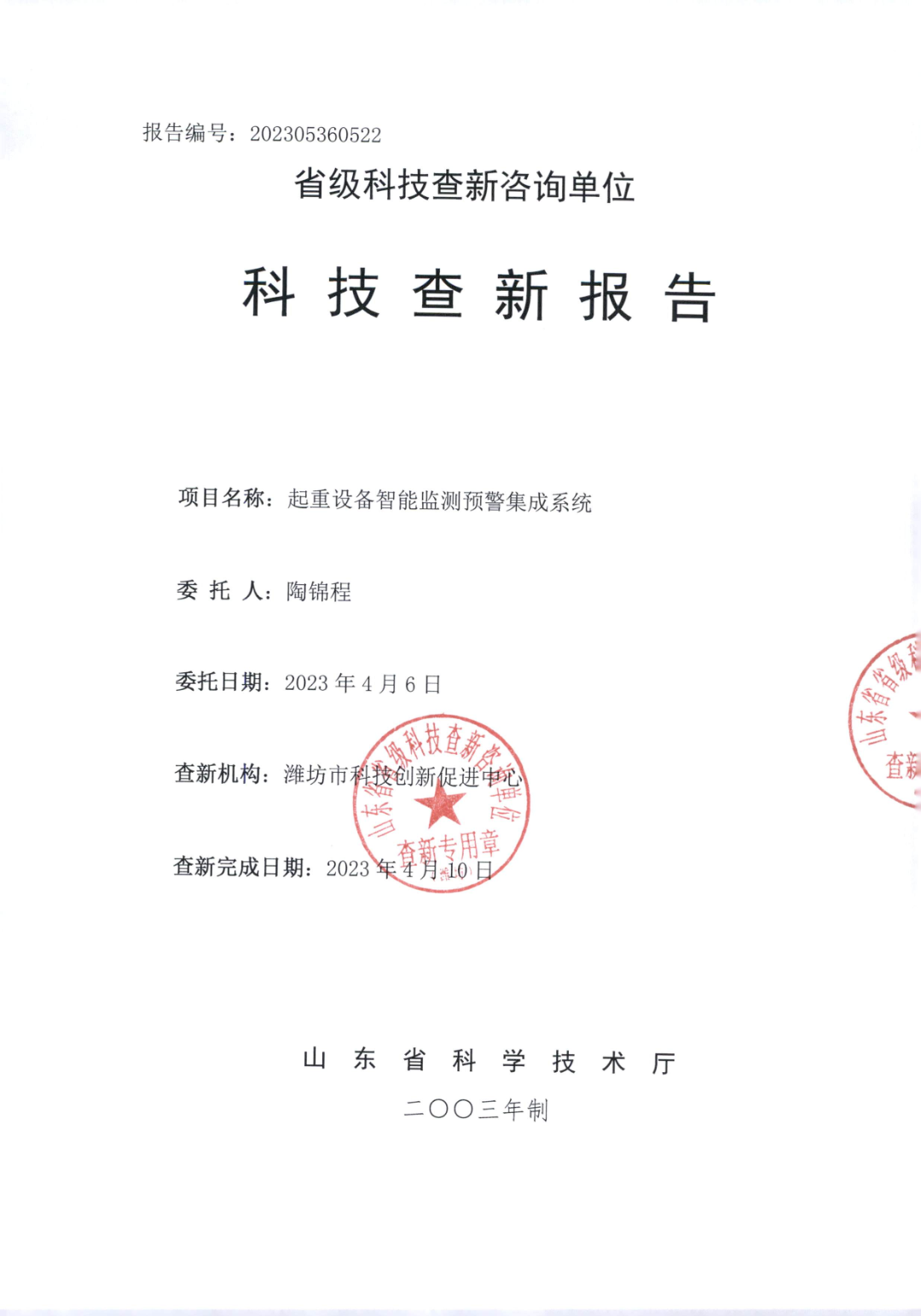
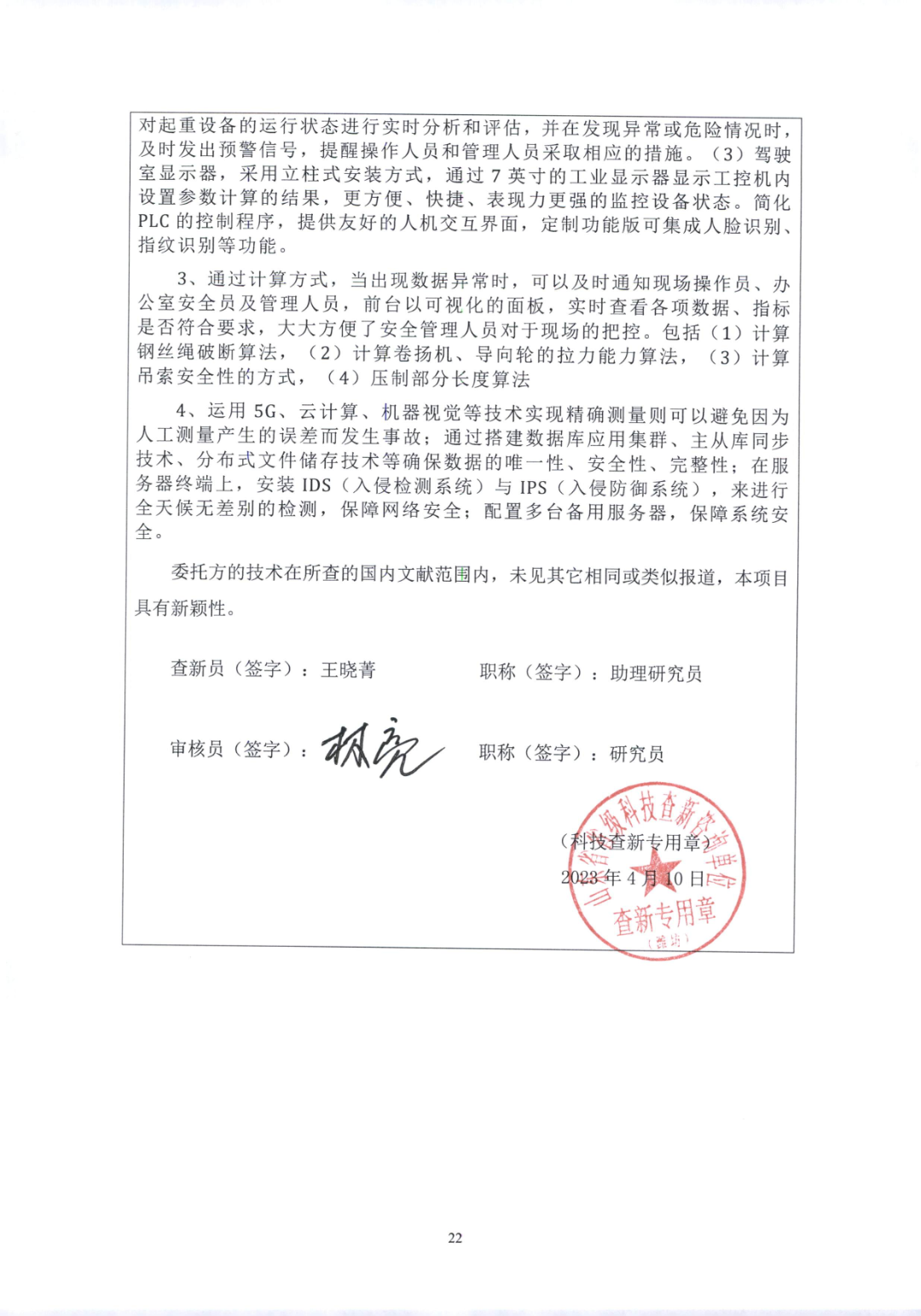
与此同时,我们整合了现有内部资源,充分发挥各部门及技术骨干的优势,由具有丰富经验的公司牵头组织,形成了高效协同的工作模式。
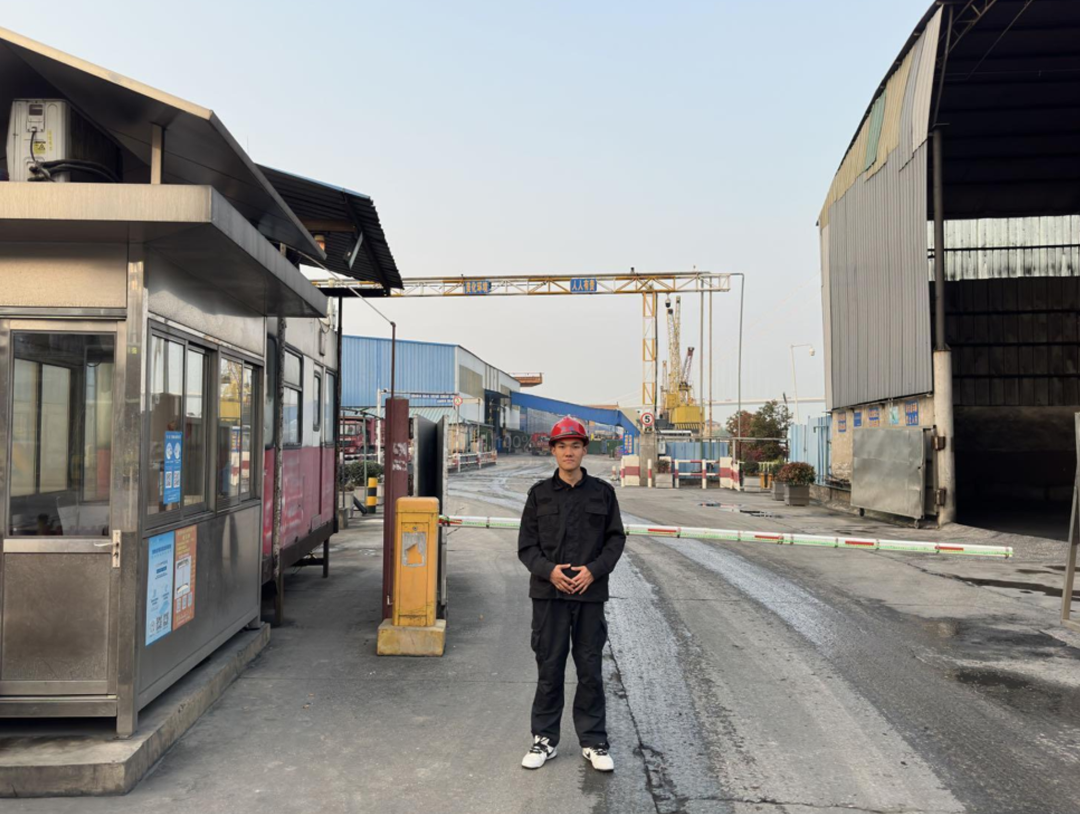
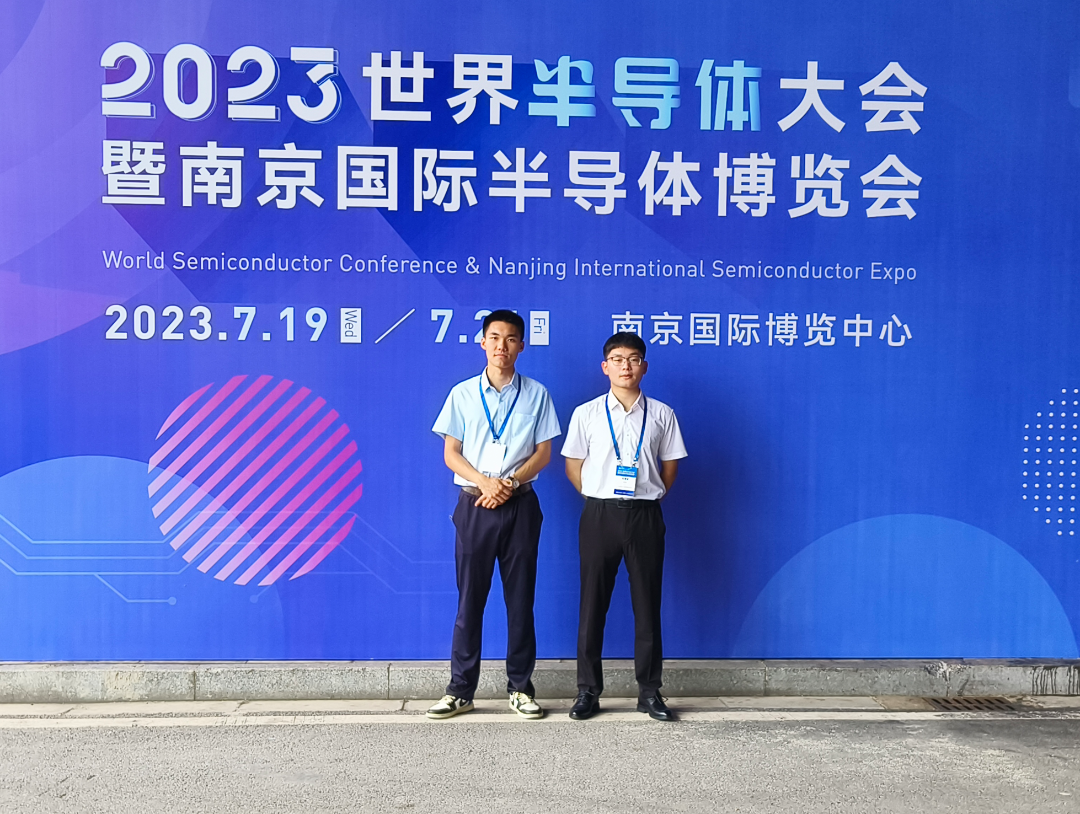
基于查新报告的有力依据,团队进一步主动对接外部资源,与多家行业领先企业、科研机构及市场推广伙伴建立了初步合作意向,共同探讨技术攻关、产品优化和商业化应用等合作模式。通过内外资源的深度融合,我们为项目的持续发展和产业化应用奠定了坚实基础。
实验室的初步成果已初见成效,为进一步验证系统在真实工作环境中的适应性和稳定性,团队决定将实验场所迁移至现场。实际环境中,设备运行状态、外界干扰及各种突发情况都成为检验产品性能的真实试金石。团队在现场精心布置测试场景,分阶段开展严格的功能测试和稳定性评估,确保每个细节都能达到预期标准。
在连续的现场测试中,系统反馈的信息逐步揭示了产品在实际应用中的潜在问题。为此,团队紧密跟进测试数据,对系统进行多轮迭代升级,不断优化算法、调整硬件配置,并针对实际操作中发现的不足进行修改和完善。每一次迭代不仅解决了部分问题,也为产品功能和性能的全面提升提供了宝贵的改进依据。
全生命周期风险管理智能协同框架致力于覆盖起重设备从设计、生产、安装、运营、维护到退役全流程的安全管理,采用人工智能和工业物联网技术,实现全链条、数字化、智能化的设备安全监控与管理。
系统通过部署多种高精度传感器,实现对设备各关键部件(如钢丝绳、吊钩、臂架、制动系统等)的实时监测,自动采集载荷、振动、温湿度、倾斜角度等数据,构建设备数字孪生模型,确保设备在整个生命周期内的运行状态全面可视化。利用云平台和边缘计算架构,所有数据实时传输与集中存储,便于后续分析和追溯。
系统集成了先进的AI算法,实现设备运行状态的动态风险评估和预测性维护。通过对历史数据和实时数据的深度学习分析,系统能够自动识别设备潜在的安全隐患和故障苗头,提前预测出关键部件可能出现的磨损、疲劳或故障风险,从而生成智能预警,并自动安排检修计划。该预测性维护功能不仅可以降低设备因突发故障导致的停机时间,还能延长使用寿命,降低维护成本。
系统还具备智能决策支持和应急响应功能。在发生异常情况时,系统能够通过大数据分析迅速判断事故原因,并生成详细的安全报告,为管理人员提供科学决策依据。同时,通过预设的应急处置预案和自动报警机制,系统能够在事故发生前或初期迅速触发应急响应,减少事故影响,确保施工和生产现场人员的安全。
生命周期安全管理系统支持全程记录与报表生成,为企业提供全面的数据支撑和合规依据。系统可自动生成设备全生命周期安全管理档案、维护记录和事故分析报告,不仅方便企业内部管理,也能满足监管部门的审查要求。通过不断优化和智能化升级,该系统为企业构建了一个闭环的安全管理生态,提升了设备运行效率和安全性,为企业节约成本、降低风险提供了有力保障。
为解决多型号设备兼容性差和数据孤岛问题,我们设计了一个开放平台架构,通过制定统一的数据格式和接口标准,实现不同品牌和型号设备的无缝对接。该平台采用开放式接口,支持多种数据协议,确保各类设备数据能够互联互通,从而打破单一制造商封闭数据带来的局限。
与此同时,团队积极推动与各设备制造商、施工企业及科研机构的合作,共同参与行业数据标准和技术规范的制定,进一步完善跨设备的数据共享机制,并通过定期兼容性测试确保平台在多种设备环境下的稳定运行。
针对智能系统无法自动适应工况的短板,我们开发了基于机器学习和数据挖掘的自适应安全阈值算法,该算法能够结合实时监测数据和历史工况动态调整安全阈值,有效避免在高温、高湿、高风速等极端环境下的误报或漏报现象。同时,通过增加环境监测模块实时采集温度、湿度、风速和地形等关键参数,为智能预警系统提供多维度数据支撑。在云平台的支持下,建立了涵盖设备状态、环境数据及历史行为的多维度预警模型,系统不断进行实时数据分析和反馈,通过持续的模拟与仿真实验,不断优化预警策略,以适应不同工况下的动态安全需求。
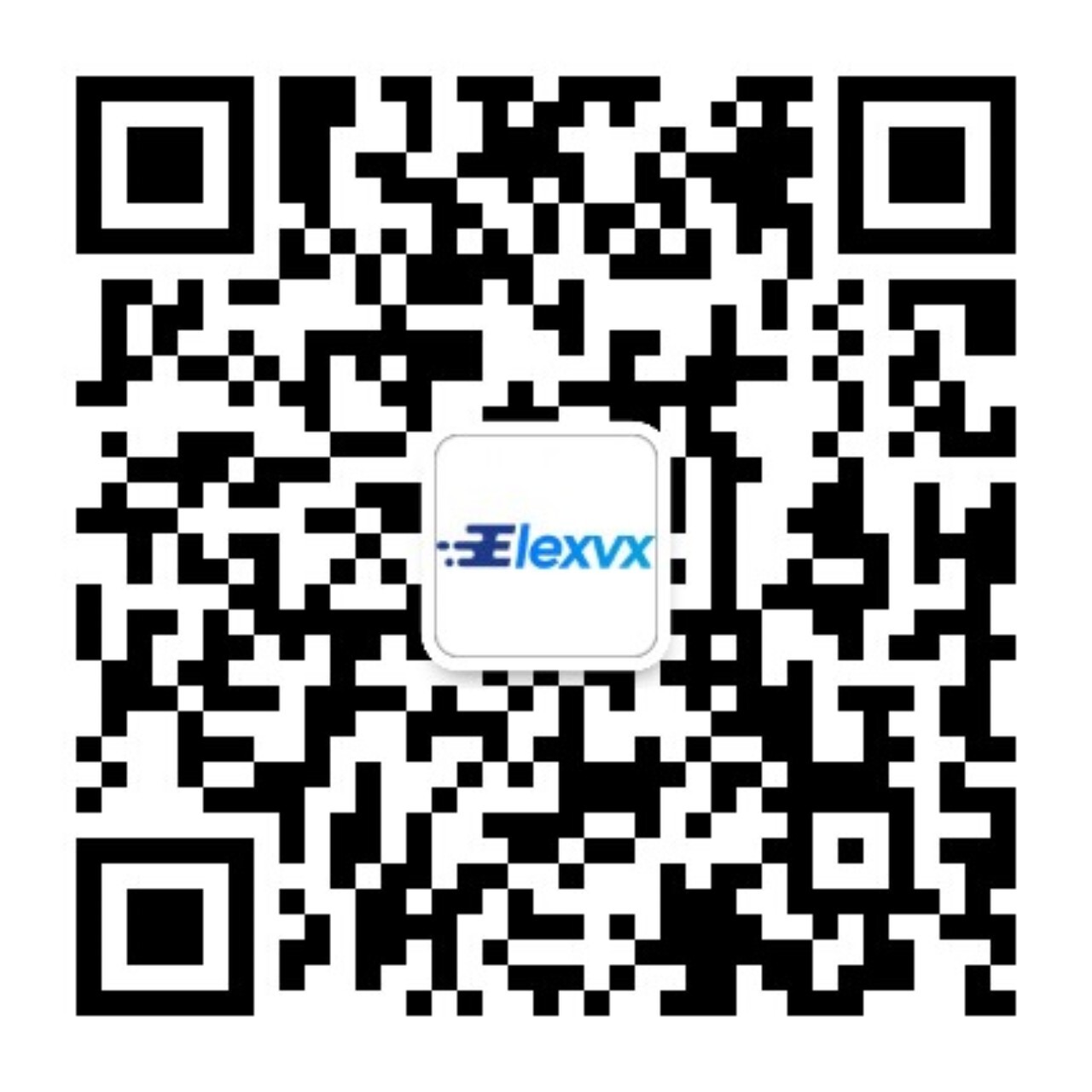